Update.
Along with the crossover chambers of my another project I made some progress in this built too. Today I assembled the Plate for Binding Post on the Back side of the Sub Enclosures. This will have my logo engraved on it.
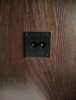
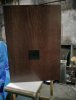
The Center hole is yet to be drilled. I did not have the required size drill bit to drill this hole. So I will purchase the same on Monday and the work will resume.
Along with the crossover chambers of my another project I made some progress in this built too. Today I assembled the Plate for Binding Post on the Back side of the Sub Enclosures. This will have my logo engraved on it.
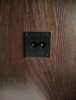
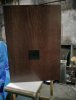
The Center hole is yet to be drilled. I did not have the required size drill bit to drill this hole. So I will purchase the same on Monday and the work will resume.